PLCs (Programmable Logic Controllers) are the foundation of current industrial automation systems. These gadgets monitor machines, processes, and manufacturing lines in a variety of sectors. So, what is a PLC exactly? In this post, we will look at the definition of PLCs, their history, main components, how they work, and where they are used. You'll also learn how PLCs continue to evolve with new technologies, shaping the future of automation.
The History and Evolution of PLC
The evolution of PLCs is a fascinating story of technological innovation that influenced modern industrial automation. From early advancements in the automobile industry to today's modern PLC systems, PLCs have evolved with growing power, flexibility, and efficiency.
Origins in the Automotive Industry
The PLC concept originated in the late 1960s, when the automotive industry sought a more dependable and adaptable solution to automate production lines. Early systems were mechanical and clunky, but the development of PLCs replaced complex relay-based systems with programmable control that could be easily tailored to the needs of varied manufacturing processes.
Technological Advances Over Decades
PLCs have evolved significantly over time. Originally developed for simple control tasks, current PLCs today have powerful processors, extended memory, and support for a variety of communication protocols. With the rise of Industry 4.0, PLCs are becoming more networked, supporting IoT devices and offering more complex capabilities in terms of analytics, machine learning, and integration with other systems.
Core Components of a PLC
A PLC system consists of several important components that work together to monitor and control industrial processes.
Central Processing Unit (CPU)
The CPU is the brain of the PLC, where all processing occurs. It runs the control program and does all necessary calculations and decisions based on the input data. The CPU also oversees communication between the PLC and other system components.
Input-Output (I/O) Modules
I/O modules are responsible for interacting with the outside world. Sensors or switches can be used as inputs to convey data to the PLC, while outputs can control devices like motors, valves, or lights. These modules are crucial for gathering real-world data and carrying out commands depending on the PLC’s program.
Power Supply Unit
The power supply unit provides the electrical power required for the PLC system. It guarantees that the system functions efficiently and reliably by converting AC power to DC power for usage by the CPU and I/O modules.
Memory & Storage
A PLC's memory contains the control program as well as data acquired while the system is in operation. It is often made up of both volatile (RAM) and non-volatile memories (EEPROM or flash memory) to make sure that data is kept even if power is lost.
Communication Interfaces
Communication interfaces allow the PLC to communicate with other devices, such as sensors, actuators, and other PLCs. These interfaces can handle a variety of protocols, including Modbus, Ethernet/IP, and Profibus, allowing easy integration into complicated automation networks.
How PLCs Work
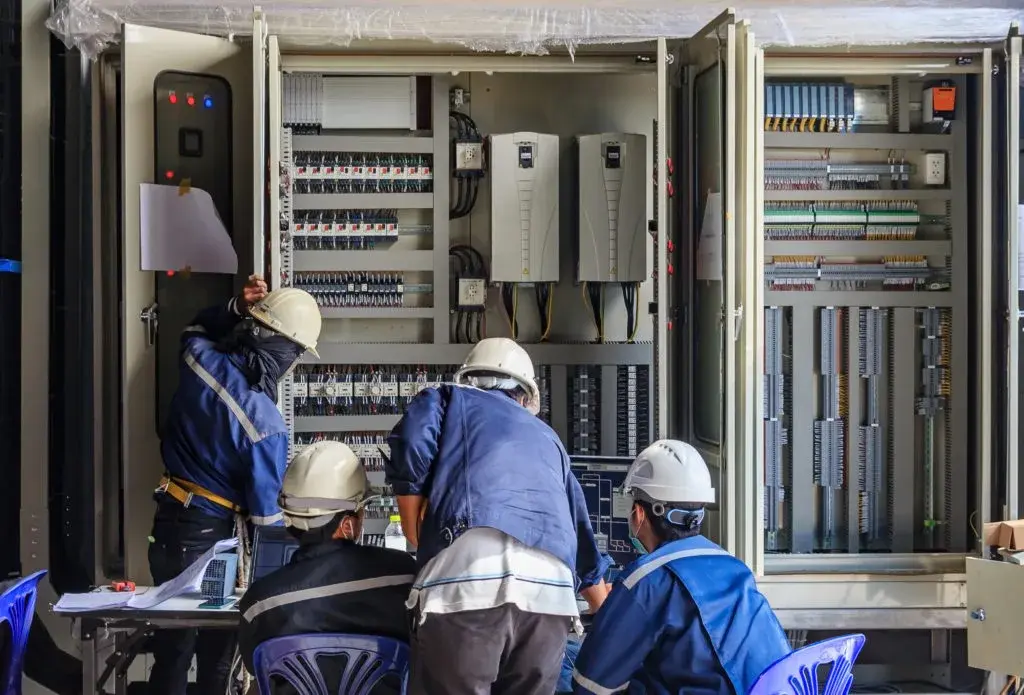
PLCs are designed to run cyclically, constantly scanning inputs, processing data, and sending outputs.
The Scan Cycle
The scan cycle, which is performed continuously, is important to PLC operation. The cycle is divided into three stages: reading inputs, executing the control program, and updating outputs. This approach enables the PLC to respond to changing situations in real time.
Programming Languages for PLCs
PLCs can be programmed in a variety of languages, including ladder logic (the most prevalent), structured text, function block diagrams, and instruction lists. Each of these languages is intended to serve a specific purpose, with Ladder Logic being the most understandable to anyone who’s familiar with electrical schematics.
Applications of PLCs in Industry
PLCs are used in a wide range of industries to automate operations and increase productivity. Here are some common applications:
Manufacturing and Assembly Lines
PLCs are commonly used on production and assembly lines to operate machines, conveyors, and robotic arms. They make sure the items are assembled correctly and effectively, with little downtime and consistent quality.
Energy and Utility
PLCs are used in the energy sector to regulate power plants, water treatment facilities, and distribution systems. They monitor variables including pressure, temperature, and flow to ensure proper functioning and prevent system breakdowns.
Transportation Systems
PLCs are also used in transportation systems to control traffic lights, railway signals, and automated toll collection systems. They help optimize traffic flow and promote safety by ensuring that systems work smoothly.
Building Automation
PLCs are used in building automation systems such as HVAC, lighting, and security to keep environmental conditions stable and safe. PLCs regulate energy consumption, monitor alarms, and control other systems to ensure a comfortable, secure, and energy-efficient facility.
Benefits of using PLCs
PLCs have various advantages in industrial automation, including flexibility, reliability, and scalability.
Flexibility and reprogrammability
PLCs are highly adaptable and may be reprogrammed to meet changes in the production process. This makes them excellent for industries that require regular changes or upgrades to their control systems.
Reliability and Durability
PLCs are designed to survive tough environments, such as excessive temperatures, vibration, and dust. Their longevity and reliability are major reasons for their employment in mission-critical applications across various industries.
Scalability
As production requirements increase, PLC systems can be simply expanded by adding extra I/O modules, memory, and communication interfaces. This scalability allows companies to expand without having to replace the entire control system.
Challenges and Considerations
While PLCs have many advantages, there are a few drawbacks to consider before implementing.
Initial Investment Costs
The initial cost of purchasing and installing a system from some
PLC manufacturers can be high, particularly for complicated operations. However, the long-term savings and increased efficiency usually outweigh the initial cost.
Complexity of Programming
Programming a PLC can be difficult, especially for people new to automation. While many PLCs employ simple programming languages such as Ladder Logic, learning how to develop good programs still requires training and skill.
Maintenance and Troubleshooting
Maintaining and troubleshooting a PLC system requires specialized expertise and training. Regular maintenance is required to guarantee that the system runs smoothly and continues to satisfy production requirements.
Future Trends in PLC Technology
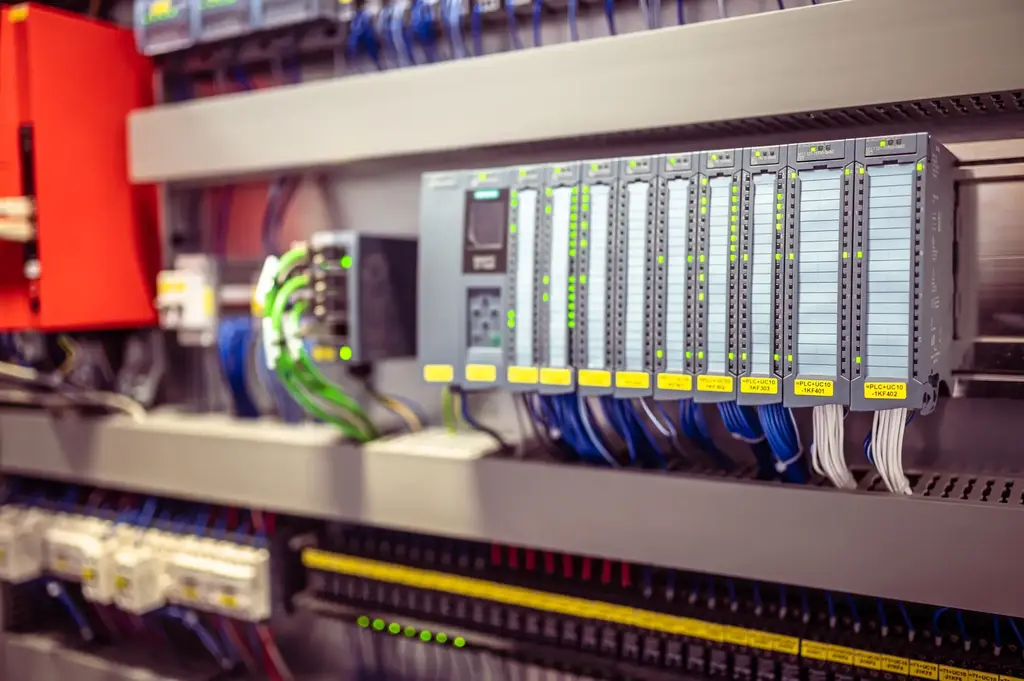
PLC technology is improving to meet modern industry expectations. Here are some of the major trends influencing the future of PLCs.
Integration with IoT and Industry 4.0
PLCs are becoming more integrated with IoT devices, allowing real-time data gathering, monitoring, and analytics. This connection contributes to Industry 4.0 objectives by providing predictive maintenance and improved decision-making.
Advancements in Programming Interfaces
New programming interfaces and tools make it easier to configure and program PLCs, decreasing the learning curve for new users while increasing productivity for experienced operators.
Improved connectivity and cybersecurity
With the advent of connected systems, PLC manufacturers are focusing more on security features. Advanced encryption, secure communication protocols, and cybersecurity measures are being used to safeguard PLCs from cyber threats.
Conclusion
PLCs are crucial to modern industrial automation since they manage a number of systems and processes. They are essential in numerous fields due to their adaptability, dependability, and scalability. PLCs will continue to be a vital component of industrial processes as automation advances.
We at BSP Automation provide premium PLC systems and components to help companies all around the world. Discover how we can increase the production and efficiency of your company by looking at our automation solutions.