Article Content
Author

Artur Solakhyan
Artur Solakhyan, freelance copywriter and editor
Understanding Safety PLCs: Principles and Applications in Industrial Automation
10 June 20255 min read

Modern industrial automation depends on complex machinery, high-speed processes, and human interaction, all of which carry risks if not managed correctly. This is why safety systems are a critical part of industrial control environments today. One of the most important pieces of this puzzle is the safety PLC. This article explains what a safety PLC is, how it works when you need one, and how it differs from a standard PLC. You’ll also learn about typical applications, benefits, and limitations, so you can decide if a Safety PLC is the right choice for your industrial setup.
What Is a Safety PLC and How Does It Work?
A safety PLC is a programmable logic controller specifically designed to carry out safety-related control functions. Unlike a standard PLC, which focuses on general automation tasks, a Safety PLC is built to handle emergency stops, guard interlocks, light curtains, two-hand controls, and other safety-critical operations.
Key Features of a Safety PLC
A typical Safety PLC includes features like redundant processors, self-checking diagnostics, and fail-safe outputs. These ensure that even if part of the system fails, the safety functions continue to operate correctly. Safety PLCs often run specialized safety-certified software and use dedicated communication protocols to maintain integrity.
For example, leading PLC brands such as Allen Bradley and Keyence provide advanced Safety PLCs that meet international safety standards.
Compliance and Standards
Safety PLCs must comply with strict international standards like IEC 61508 and ISO 13849, which define the safety integrity levels (SIL) or performance levels (PL) required for functional safety. This means every part of the design, from hardware to software, must pass rigorous tests and certifications to ensure it performs correctly under fault conditions.
Safety PLC vs Standard PLC: Key Differences
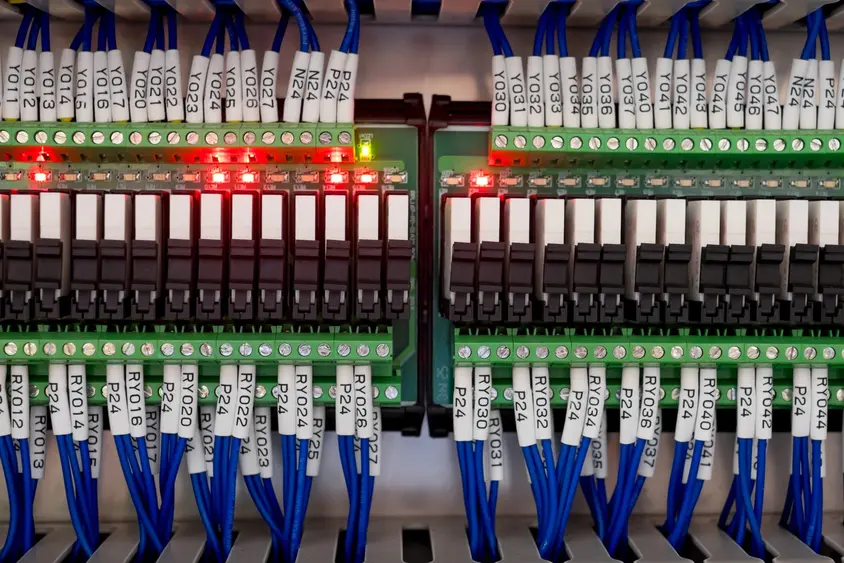
Understanding the difference between a safety PLC and a standard PLC helps manufacturers decide which to use for each task.
Hardware and Software Differences
A standard PLC controls routine machine operations, such as conveyors, pumps, and actuators, but is not safety-certified. A safety PLC adds extra layers: redundant processors, safe input/output modules, and robust self-testing cycles. It constantly checks its internal circuits and communication lines for errors.
The software used in Safety PLCs is validated to ensure it can’t be accidentally altered in ways that could compromise safety. For example, safety logic often runs separately from the general automation logic to prevent conflicts.
Functional and Use Case Comparison
In a typical factory, a standard PLC might manage motor speed, temperature, and sequence logic. Meanwhile, a Safety PLC handles the PLC safety circuit that shuts down the system if a worker opens a guard door or triggers an emergency stop.
When Is a Safety PLC Required?
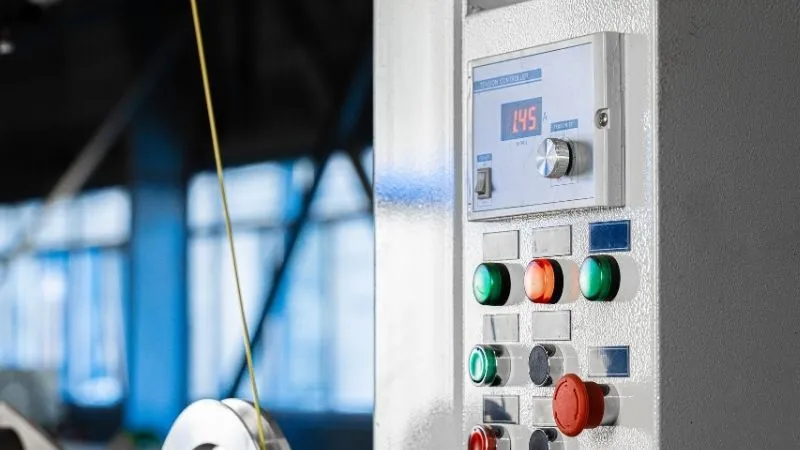
So, when is a safety PLC required? The short answer: whenever people interact with machinery that poses a risk of injury or worse. Many applications legally require a safety PLC, but even when not mandatory, it’s often the safest and smartest choice.
High-Risk Industrial Environments
Factories using high-speed cutting machines, presses, or heavy robots benefit from Safety PLCs. In these environments, unexpected errors or malfunctions could lead to severe injuries or significant equipment damage.
Legal and Regulatory Triggers
Certain industries and countries mandate the use of Safety PLCs when machinery reaches a specific hazard level. Regulations like OSHA in the US and the Machinery Directive in the EU often push companies to adopt compliant safety control systems to protect workers.
Human-Machine Collaboration
Collaborative robots (cobots) and modern production lines rely heavily on workers and machines sharing the same workspace. Safety PLCs help monitor these interactions, ensuring equipment stops instantly if a hazard occurs.
Conditions That Make Safety PLCs Essential
Knowing when a Safety PLC is needed depends on more than just a checklist; it’s about understanding the real risks that come with specific equipment and environments. While some simple machines may run safely with traditional hardwired relays, modern production often demands flexible safety logic that only a certified Safety PLC can handle.
For example, in industries where production lines change frequently or equipment is reconfigured for new products, rewiring hardwired safety circuits every time is costly and slow. A Safety PLC lets engineers adjust safety parameters through the software while maintaining compliance with required SIL or PL levels. This saves time and ensures that every machine modification stays within safe operating limits.
Beyond hardware needs, companies must also consider how people interact with machines. If workers frequently enter hazardous zones for maintenance, changeovers, or inspections, a Safety PLC makes it easier to manage interlocks, two-hand controls, and zone monitoring. This level of control is critical for ensuring the system reacts instantly when a gate opens or an emergency stop is pressed.
High-Risk Machinery and Processes
Heavy machinery like stamping presses, large conveyor systems, and robotic welding cells present serious risks if left unprotected. These machines often operate at high speeds or with enough force to cause severe injuries if something goes wrong. A standard PLC may run the basic machine logic, but it cannot guarantee that the system will stop safely in an emergency.
A safety PLC adds extra layers of protection, constantly checking the state of safety inputs and ensuring that the machine can shut down immediately if needed. Redundant circuits and fail-safe outputs mean that even if part of the system fails, the safety response works as intended. Many facilities combine safety PLCs with advanced safety devices like light curtains, pressure-sensitive mats, or safety scanners to create a comprehensive PLC safety circuit that reacts to real-world hazards in real-time.
Regulatory Requirements
Safety standards continue to tighten worldwide, making it more important than ever to understand when a safety PLC is required by law. Local and international regulations often dictate what type of control system is acceptable for certain machinery. For example, European manufacturers must comply with the Machinery Directive, which references ISO 13849 and IEC 62061 for functional safety.
Many industries follow risk assessments to decide which SIL or PL level is needed based on the severity of potential harm, frequency of exposure, and likelihood of avoiding danger. Higher levels of risk often mean that simple, hardwired relays are not enough to achieve compliance. Instead, a certified Safety PLC with redundant processing and validated software becomes the practical and legal choice.
Failing to meet these requirements can lead to fines, shutdowns, or worse, serious accidents that damage a company’s reputation and put people in danger. Working with an experienced industrial automation parts distributor helps ensure your system includes the right certified components from trusted PLC brands.
Applications in Industrial Automation
Safety PLCs are now standard in many industries because they combine flexibility and reliability. They allow companies to scale operations, adapt production lines, and integrate new machinery without sacrificing safety.
Manufacturing and Robotics
In high-volume manufacturing, safety PLCs control vital safety functions like emergency stop circuits, guard locking mechanisms, and two-hand control stations for presses or injection molding machines. Modern robot cells rely on Safety PLCs to monitor zone scanners and light curtains that stop robotic arms when a worker steps inside a restricted area.
Unlike static safety relays, safety PLCs can handle multiple safety zones and complex logic at once. This is especially important when robots and humans work side by side on assembly lines. By using a flexible PLC safety circuit, manufacturers keep operators safe while maintaining high productivity.
Material Handling and Logistics
Safety PLCs are equally important in warehouses, distribution centers, and automated storage facilities. Large conveyor systems, sorting lines, and palletizing robots create many points of contact where people may need to step in. With a safety PLC, companies can program safe shutdowns and interlocks for multiple access points.
For example, when a technician opens a maintenance gate on a conveyor, the safety PLC instantly halts the motor and ensures that no restart happens until the gate is fully closed and locked. Integrated safety devices like light curtains, area scanners, or pressure mats send real-time data to the safety PLC, which processes these signals and takes immediate action. This guarantees that material flow stays efficient without compromising worker safety.
Process Industries
In chemical, oil and gas, or pharmaceutical production, safety risks include leaks, overpressure, or dangerous chemical reactions. A failure in these systems can have catastrophic consequences, which is why safety PLCs play a crucial role in monitoring and controlling critical points.
These industries often require continuous monitoring of pressure, temperature, and flow, with automatic shutoffs if conditions drift beyond safe limits. A safety PLC’s redundant processors and self-checking diagnostics ensure that even during a fault, emergency shutdown procedures activate correctly. Compared to basic hardwired safety circuits, a safety PLC offers real-time status reports and alarms, giving engineers the data they need to keep plants running safely and legally.
Benefits and Limitations of Safety PLCs
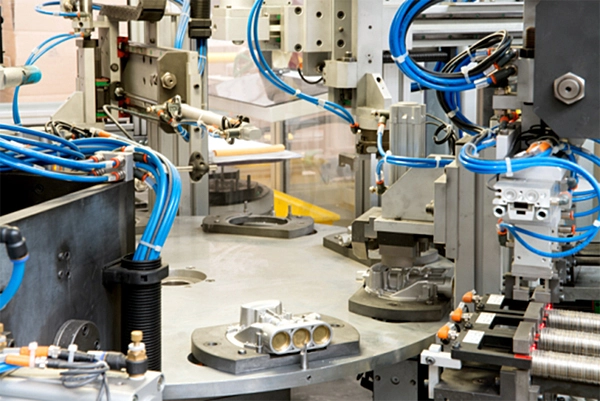
Every investment comes with trade-offs. Let’s take a look at what makes safety PLCs valuable and what to consider before you choose one.
Key Advantages
- Enhanced worker protection: A safety PLC’s main role is to protect human life and health.
- Compliance: Using certified safety PLCs helps companies meet legal obligations and pass inspections.
- Flexibility: Unlike hardwired safety relays, safety PLCs make it easier to modify safety logic through software updates.
- Diagnostics and Monitoring: Advanced self-checks make it simpler to spot faults before they cause downtime.
- Integration: Modern safety PLCs work well alongside standard PLCs, helping you manage both safety and standard controls in one network.
Potential Challenges
- Higher upfront costs: Safety PLCs are more expensive than standard controllers due to their certifications and redundancy features.
- Complex setup: Programming and validating safety logic requires skilled engineers and proper documentation.
- Maintenance: Extra diagnostics and checks mean teams need to stay on top of updates and periodic validation.
Conclusion
A safety PLC is much more than a standard controller; it’s a dedicated safeguard for your workers, equipment, and business. From manufacturing robots to hazardous chemical plants, safety PLCs provide the reliability and compliance that keep modern industries running safely.
Whether you run heavy machinery, collaborative robots, or high-speed packaging lines, it pays to ask: When is a safety PLC required in your operation? If you’re unsure, consult experts to choose the right controller that complies with all safety standards.
BSP is your trusted industrial automation parts distributor for the world’s leading PLC brands and industrial automation brands, including certified safety PLCs and related components. Our team is ready to help you build safer, more productive systems with the right hardware and expertise.
FAQ
Have a question?
If you didn't find the automation part you were looking for, our support team is here to help. Just contact us, and we'll do our best to source the exact part you need. We're committed to meeting your needs and ensuring your satisfaction.