Understanding PLC Inputs: Types, Functions, and Industrial Applications

Freelance copywriter and editor

Programmable Logic Controllers (PLCs) rely on accurate inputs to communicate with the real world and control automated processes. These inputs are essential components that allow a PLC to monitor changes in equipment, receive data from field devices, and execute logical operations. In industrial automation, PLC inputs and outputs form the communication bridge between machinery and control systems. Understanding how these components work helps engineers operate efficiently and safely across various sectors. This guide covers the different types of inputs, their functions, industrial uses, and best practices for integration.
What are PLC Inputs?
PLC inputs are signals received by the controller from field devices such as sensors, switches, and measuring instruments. These inputs inform the PLC about real-time conditions in the process environment. The controller processes the information and makes decisions based on its programmed logic. This allows precise control of machinery and equipment in automated systems.
Role of Inputs in PLC Systems
Inputs serve as the data entry point for a system. Whether it’s a button being pressed or a temperature sensor reaching a threshold, inputs communicate these events to the controller. The PLC continuously scans its input terminals to detect any changes and updates its internal logic accordingly.
Importance in Industrial Automation
In automated systems, timely and accurate input signals are vital. They ensure that processes respond to changes in physical conditions such as pressure, flow, or position. A reliable input setup contributes to operational efficiency, system safety, and reduced downtime across production lines and industrial machines.
Types of PLC Inputs
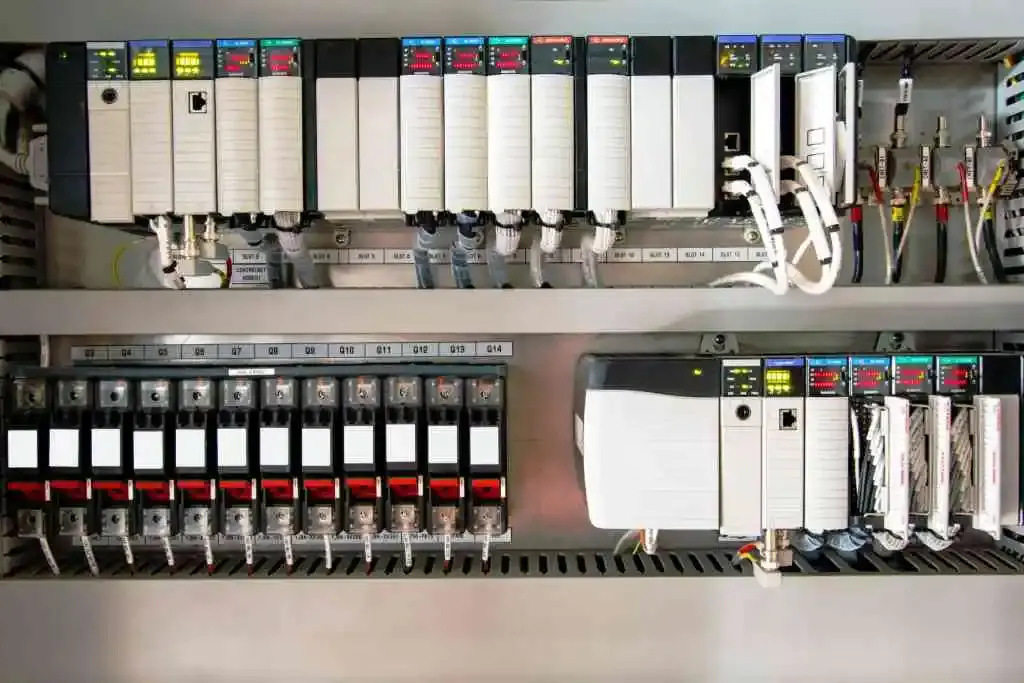
PLCs support various inputs to match the needs of different applications. These inputs can be classified into three major categories: digital, analog, and specialized.
Digital (Discrete) Inputs
Digital inputs detect binary conditions – ON or OFF, 1 or 0. Examples include push buttons, limit switches, and proximity sensors. These inputs are commonly used in systems that require simple state monitoring, such as conveyor belt activation or door status detection.
Analog Inputs
Analog inputs process variable signals such as voltage or current. Devices like thermocouples, pressure transmitters, and flow sensors send continuous signals that reflect changing conditions. These inputs are used in applications requiring measurement, regulation, or feedback control.
Specialized Inputs
Some systems require high-speed counters, encoder feedback, or pulse detection. These specialized inputs handle more complex or time-sensitive data. They’re essential in motion control, material tracking, and high-speed packaging operations.
Functions of PLC Inputs
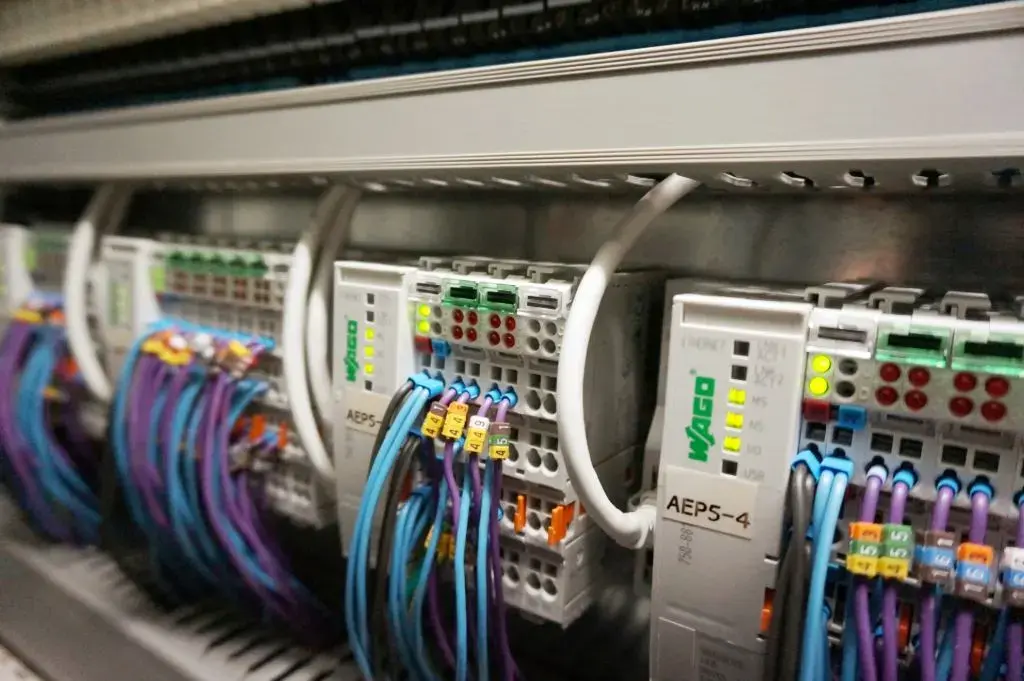
Understanding the functions of PLC inputs helps ensure reliable system performance across various industrial applications. Each input signal must go through several key steps from the moment a field device detects it to the point it influences decision-making within the logic. These stages are crucial in determining how accurately the system can respond to real-world conditions. Whether it's controlling a motor or managing a complex process, proper input handling allows the controller to make fast, accurate decisions that align with operational goals.
Signal Acquisition
The first step in handling any PLC input is signal acquisition. This refers to the process of detecting a physical signal from a connected field device, such as a proximity sensor or temperature transmitter. The input module reads the incoming signal and determines its status. This might involve checking whether a switch is open or closed, or measuring the voltage level coming from an analog device. The accuracy and reliability of this acquisition step are vital because any incorrect or missed input can disrupt the logic cycle and cause system errors or downtime.
Signal Conditioning
After the signal is acquired, it often requires conditioning before it can be processed effectively by the PLC. Signal conditioning involves improving the signal quality through filtering to remove electrical noise, isolating the signal to protect the controller from voltage spikes, or converting the signal into a range or format that matches the PLC’s input requirements. This step ensures that the signal is not only readable but also accurate and safe for interpretation. For example, analog signals from field devices may need to be converted from 0–10V to a 4–20mA current range, depending on system standards.
Data Interpretation
The final stage is data interpretation, where the PLC processes the conditioned signal based on the control logic programmed by engineers. The controller evaluates the input to determine what action, if any, is required. This could involve turning a machine on or off, adjusting a process variable, or triggering an alarm. The PLC continuously checks input status, comparing new values to setpoints or thresholds. Accurate interpretation allows for consistent automation and reduces the chances of system faults, delays, or safety hazards in critical applications.
Industrial Applications of PLC Inputs
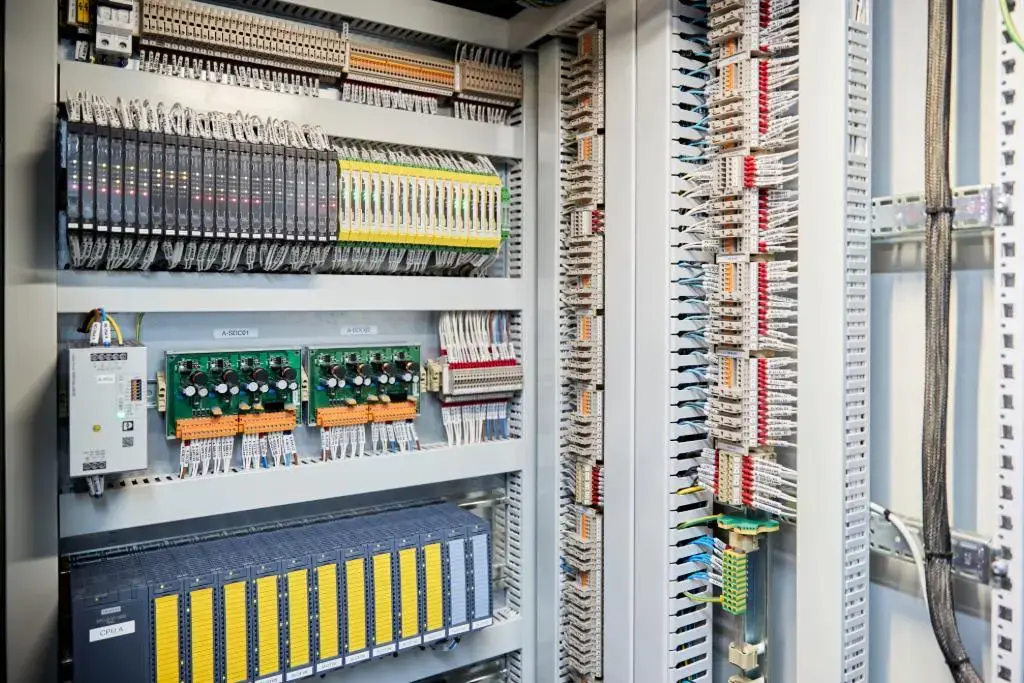
PLCs are widely used in modern industries, and each sector relies on accurate, real-time inputs to support its operations. Whether it's controlling motors, monitoring flow rates, or managing batch production, PLC inputs and outputs form the foundation of decision-making in automated processes. Below are several examples of how these inputs apply across different sectors, showing their significance in maintaining productivity and safety.
Manufacturing
In the manufacturing sector, digital inputs often detect machine states, part positions, or human interactions through sensors like limit switches and push buttons. These inputs are essential for initiating sequences, detecting jams, or controlling conveyors. Analog inputs, on the other hand, gather data from devices that monitor speed, vibration, or temperature. This allows production systems to respond to fluctuations and maintain high levels of accuracy and product consistency. PLCs are also used in machine safety systems, where inputs play a role in emergency stop conditions and access control.
Process Industries
In industries such as food and beverage, chemical processing, and pharmaceuticals, analog inputs are commonly used to monitor and regulate variables like pressure, temperature, flow, and tank levels. These industries depend on continuous measurement and feedback to ensure product quality and compliance with safety standards. Inputs from level sensors, pH meters, or pressure transmitters are interpreted by the PLC to make constant adjustments to pumps, valves, or heating elements. Digital inputs are also involved in starting and stopping machinery, enabling safe and efficient production cycles.
Energy Sector
Within the energy sector, PLCs manage everything from power generation to distribution. Inputs from current transformers, voltage sensors, and position switches provide the controller with information needed for real-time decisions. Analog inputs track load demand, voltage levels, or fuel flow in generation stations, while digital inputs monitor breaker status, equipment availability, or fault conditions. Accurate inputs help maintain grid stability, avoid equipment failures, and coordinate emergency responses. These systems must operate with high reliability to ensure uninterrupted energy delivery.
Best Practices for Implementing PLC Inputs
Proper implementation of PLC inputs ensures accuracy, reliability, and long-term system performance. Simply connecting devices is not enough. Best practices must be followed to minimize signal noise, prevent wiring errors, and maintain system efficiency over time. Below are essential guidelines for the successful deployment and ongoing maintenance of PLC input systems.
Proper Wiring and Shielding
Correct wiring and shielding protect input signals from interference and lower the chances of signal degradation. For analog inputs, especially, use shielded cables to block electromagnetic noise from nearby equipment such as motors or power lines. Ground shielding at a single point to avoid loops, and route input wires away from high-voltage cables. Proper labeling of wires helps during installation and troubleshooting, while the use of terminal blocks and cable trays contributes to a clean and organized control panel layout.
Regular Maintenance
Routine inspection and maintenance of input components prevent signal errors and unplanned downtime. Check for loose terminals, damaged wires, corroded contacts, or physical wear on sensors. Regular cleaning and testing ensure that field devices operate within expected ranges and that the PLC receives accurate data. Maintenance logs and scheduled checks make it easier to catch developing problems early. Keeping spares for critical input devices can also minimize disruption during replacements.
Documentation
Thorough documentation is the key to supporting input system performance over the long term. Maintain detailed records of all connected input devices, their locations, wiring diagrams, signal types, and reference values. This makes troubleshooting more efficient and helps during system modifications or upgrades. Clear documentation also supports training for new technicians and ensures continuity in maintenance and system understanding. A well-documented input structure is a valuable resource for minimizing errors and improving response times.
Conclusion
PLC inputs are the foundation of reliable control systems in industrial environments. From capturing sensor data to activating processes, each input plays a critical role. Knowing the types, functions, and best practices for implementation ensures accurate communication between field devices and the controller.
For companies seeking dependable industrial automation parts, BSP Automation supplies components from world-renowned PLC manufacturers, offering expert guidance and high-quality solutions tailored to your operational needs. Visit our homepage to learn more or contact us for consultation.
FAQ
If you didn't find the automation part you were looking for, our support team is here to help. Just contact us, and we'll do our best to source the exact part you need. We're committed to meeting your needs and ensuring your satisfaction.